Airgap thickness
Distance between the rotor surface and stator surface.
The airgap thickness is defined as the distance between the rotor and stator surfaces as shown in Fig. 1. The thinner the airgap thickness, the larger the airgap flux density and the generated force. However, reducing the airgap thickness does also increase the cogging torque!
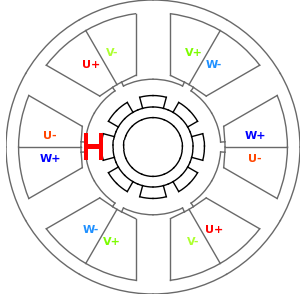
Fig. 1 Illustration of the airgap thickness on the example of an 8 pole 6 slot machine with a double-layer concentrated winding (airgap thickness is exagerated for clarity).
The airgap thickness should be chosen large enough in order to ensure that the stator and rotor are not touching mechanically. Practically feasible values for the airgap thickness depend on a large range of parameters, such as: Unbalanced forces, manufacturing tolerances, motor assembly, choice of bearings, eventual rotor bandages, stiffness of the rotor, size of the machine, etc.
According to Hanselman, "Brushless Permanent-Magnet Motor Design", McGraw-Hill Inc. 1994, manufacturing tolerances do not allow the physical airgap thickness to get much smaller than approximately 0.3mm (0.012 in).
Say, "The performance and design of alternating current machines", Pitman 1948, provides the following equation for the minimum possible airgap thickness as a function of the airgap diameter $D$ and the machine length $L$ (all parameters provided in 'm'):$$0.0002 + 0.003 \sqrt{\frac{DL}{2}}$$
Read about another glossary term